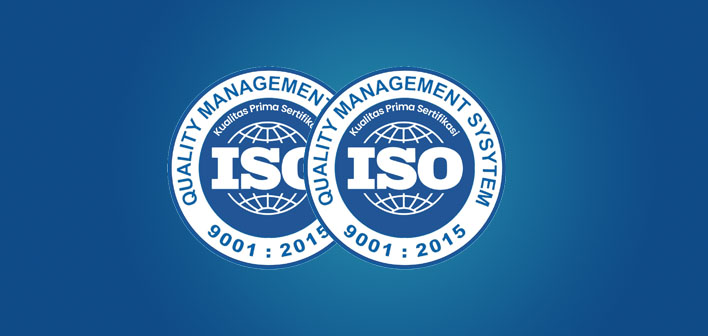
ISO 9001 Quality Management Standard
ISO 9001 is an international standard that sets out the criteria for a Quality Management System (QMS).
We provide ISO 9001 implementation consultation.
Partner with Bitlion to implement ISO 9001 and future-proof your operations.
Start with a free consultation — reach out to Bitlion today!
💡 What Is ISO 9001?
🔍 In Simple Terms
ISO 9001 is an international standard that sets out the criteria for a Quality Management System (QMS).
Think of it as a global playbook for companies that want to consistently deliver quality products and services, improve customer satisfaction, and keep getting better over time.
👥 Who Creates It?
ISO 9001 is published by the International Organization for Standardization (ISO) — a global body made up of national standards organizations. The most current version is ISO 9001:2015, which replaced the 2008 version.
🏗️ The Core of ISO 9001: Quality Management System (QMS)
At the heart of ISO 9001 is the Quality Management System, which is basically a structured way of doing things to ensure your organization can:
Meet customer and regulatory requirements
Continually improve
Prevent errors rather than just fixing them after they occur
📋 A QMS Includes:
Policies
Processes
Procedures
Roles and responsibilities
Continuous improvement mechanisms
🎯 Key Principles of ISO 9001
The standard is built around 7 quality management principles, which guide how organizations should operate:
1. Customer Focus
Understand customer needs
Strive to exceed expectations
Improve customer satisfaction
2. Leadership
Create a clear vision
Establish unity of purpose
Lead by example
3. Engagement of People
Empower employees
Recognize their contributions
Encourage involvement at all levels
4. Process Approach
Understand how activities are linked
Manage processes as a coherent system
Increase efficiency and effectiveness
5. Improvement
Be proactive about change
Encourage innovation
Continuously raise the bar
6. Evidence-Based Decision Making
Use data and metrics
Make informed decisions
Evaluate outcomes
7. Relationship Management
Build strong supplier relationships
Manage external and internal partnerships
Focus on long-term success
📦 What Are the Requirements?
ISO 9001 includes a number of mandatory requirements that organizations must meet to get certified. These are grouped into 10 clauses:
✅ Clauses 1 to 3: Introductory
Scope
Normative references
Terms and definitions
🧩 Clauses 4 to 10: The Actual QMS Requirements
Here’s a quick peek:
Clause 4: Context of the Organization
Understand internal and external issues
Identify stakeholders
Define the scope of your QMS
Clause 5: Leadership
Top management commitment
Quality policy
Assign roles and responsibilities
Clause 6: Planning
Risk-based thinking
Set quality objectives
Plan changes properly
Clause 7: Support
Resources and infrastructure
Competency and awareness
Documented information
Clause 8: Operation
Planning and controlling processes
Customer communication
Product/service delivery
Clause 9: Performance Evaluation
Monitor, measure, and analyze
Conduct internal audits
Review performance
Clause 10: Improvement
Handle nonconformities
Use corrective actions
Drive continuous improvement
🏆 Why Get ISO 9001 Certified?
So, why do so many companies chase ISO 9001 certification?
🚀 Benefits Include:
Improved efficiency and productivity
Increased customer satisfaction
Stronger employee engagement
International recognition
Better risk management
Stronger supplier relationships
A culture of continuous improvement
And yes, it can also be a great marketing tool — it tells your customers you’re serious about quality.
🔧 How Does Certification Work?
ISO itself doesn’t certify organizations. Instead, independent certification bodies perform audits and issue certificates.
🧭 Steps to Certification:
Gap Analysis
– Compare your current system with ISO 9001 requirements
Implementation
– Document and apply new processes, train your team
Internal Audit
– Check how things are running before an external audit
Management Review
– Leadership evaluates system effectiveness
Certification Audit (Stage 1 & 2)
– Conducted by an external auditor
Surveillance Audits (Annually)
– Ensure you're still compliant
🏢 Who Uses ISO 9001?
It’s not just for manufacturing companies!
👇 Industries That Use ISO 9001:
Healthcare
Education
IT and software development
Construction
Food and beverage
Financial services
Government agencies
Big or small, public or private — any organization can implement ISO 9001.
💬 Common Myths About ISO 9001
Let’s bust a few misconceptions:
❌ "ISO 9001 is only for big corporations."
→ Truth: Small businesses can (and do) benefit greatly.
❌ "It’s just about documentation."
→ Truth: Documentation is a part of it, but process improvement and customer satisfaction are the real focus.
❌ "Once certified, you’re good forever."
→ Truth: Certifications require regular audits and ongoing improvement to maintain.
📈 ISO 9001 and Business Growth
ISO 9001 isn’t just a certificate you hang on the wall. When implemented correctly, it becomes part of your business culture, driving:
Better decision-making
Less rework and waste
Happier customers
More trust from partners and regulators
🎓 Final Thoughts
ISO 9001 is more than just a checklist. It’s a philosophy of doing things better, consistently, and with the customer in mind.
Whether you're just learning about it or planning to get certified, ISO 9001 is a strong foundation for building an efficient, resilient, and trusted organization.
🔵 Phase 1: Planning & Preparation
Step 1. Understand ISO 9001 Requirements
🔲 Review ISO 9001:2015 standard document
🔲 Identify the 7 Quality Management Principles
🔲 Determine applicability to your organization
🔲 Assign a project leader or ISO coordinator
Step 2. Conduct a Gap Analysis
🔲 Compare current processes against ISO 9001 clauses
🔲 Identify missing or non-compliant areas
🔲 Document existing documentation and practices
🔲 Prioritize areas for improvement
Step 3. Define Scope & Objectives
🔲 Define the scope of the Quality Management System (QMS)
🔲 Identify internal & external issues (Clause 4.1)
🔲 Determine interested parties and their needs (Clause 4.2)
🔲 Set quality objectives (Clause 6.2)
Step 4. Obtain Top Management Commitment
🔲 Hold briefing with leadership on ISO 9001 benefits
🔲 Secure budget and resources for the project
🔲 Assign roles and responsibilities
🔲 Develop and communicate a quality policy (Clause 5.2)
🟠 Phase 2: System Design & Documentation
Step 1. Map Core Business Processes
🔲 Identify key processes and subprocesses
🔲 Develop process flowcharts or diagrams
🔲 Define inputs, outputs, responsibilities, and risks
🔲 Assign process owners
Step 2. Develop Required Documents
🔲 Quality Manual (optional under 2015 but still useful)
🔲 Documented Procedures (e.g., control of documents, nonconformities)
🔲 Work Instructions or SOPs
🔲 Control of documented information (Clause 7.5)
Step 3. Define QMS Policies
🔲 Quality Policy
🔲 Risk Management & Opportunity Assessment
🔲 Change Management
🔲 Customer Communication & Complaint Handling
Step 4. Train Employees
🔲 Conduct ISO 9001 awareness training
🔲 Train employees on their role in the QMS
🔲 Provide process-specific training
🔲 Ensure competency records are documented
🟡 Phase 3: Implementation & Operation
Step 1. Implement QMS Processes
🔲 Roll out updated procedures across departments
🔲 Begin using forms and records (e.g., audit checklists, training logs)
🔲 Monitor and control operational processes (Clause 8)
🔲 Ensure communication of QMS throughout the organization
Step 2. Manage Risks and Opportunities
🔲 Identify process risks and opportunities (Clause 6.1)
🔲 Implement control actions
🔲 Document risk assessment outcomes
🔲 Review risks during management review
Step 3. Monitor and Measure Performance
🔲 Define performance indicators for processes
🔲 Track customer satisfaction metrics
🔲 Review feedback and complaints
🔲 Conduct regular reviews of performance data
Step 4. Conduct Internal Audits
🔲 Prepare an internal audit plan
🔲 Train internal auditors (if needed)
🔲 Perform audits of each process
🔲 Record findings and issue corrective actions
🟢 Phase 4: Certification & Continuous Improvement
Step 1. Conduct Management Review
🔲 Schedule and hold management review meeting (Clause 9.3)
🔲 Review audit results, performance metrics, risks, and objectives
🔲 Identify improvement opportunities
🔲 Record decisions and action items
Step 2. Apply for Certification
🔲 Choose an accredited ISO certification body
🔲 Submit application and required documentation
🔲 Schedule Stage 1 (document review) audit
🔲 Prepare for and schedule Stage 2 (full QMS) audit
Step 3. Address Audit Findings
🔲 Respond to nonconformities with root cause analysis
🔲 Implement corrective actions
🔲 Submit evidence to auditor (if required)
🔲 Receive ISO 9001 certificate
Step 4. Maintain & Improve QMS
🔲 Monitor compliance and process effectiveness
🔲 Update documentation when needed
🔲 Conduct regular internal audits and reviews
🔲 Drive continual improvement (Clause 10)